EHEDG Guideline 65, 'Sampling Systems for Representative Liquid Sampling' | New available guideline
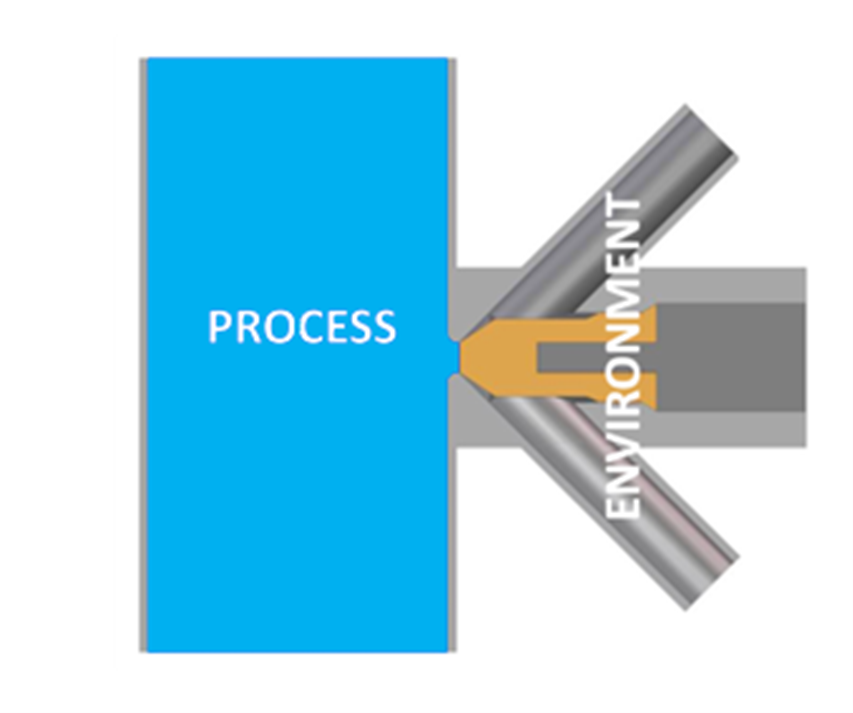
Now available in our catalogue
EHEDG has released Guideline 65, ‘Sampling Systems for Representative Liquid Sampling’, a comprehensive document focused on the hygienic design, correct installation, operation and maintenance of sampling systems in liquid food processing. This guideline is pivotal in ensuring that samples taken are truly representative of the liquid product, while also preventing cross-contamination of the process.
To further explore the development and significance of this new publication, we spoke with Carsten, who shared valuable insights into the motivation behind the guideline and its practical applications across the industry.